Mechanical Draft
Crossflow Replacements
BACKGROUND
Two 12 cell crossflow mechanical draft cooling towers at a major western United States coal fired power plant (1037 MW) required replacement of one half of each tower to ensure plant operational reliability (the other half of each had been recently replaced in previous outages). The work was completed in two phases; each during a planned outage in the fall of a two year period. ATS was issued a contract to replace 6 cells of each existing wood framed cooling tower with new state of the art crossflow cooling tower cells including engineered pultruded fiberglass structures. This type of project is commonly referred to as “Knockdown and Replace”. The work was completed in two phases. Each phase occurred during a planned outage in the cooler months of a two year period.
PROJECT CHALLENGES
The schedule for each phase of this project represented the major challenge to be overcome for successful completion. In order to meet the schedule, the demolition activities had to be performed very quickly by using a “track hoe” or “excavator” to literally knock the tower down and then to clean all debris from the cooling tower cold water basin/foundation. In this process, an experienced operator was employed to insure minimal damage to the foundation of the cooling tower.
Once the re-erection activities begin, a technique known as “Bent Line” erection was used to hoist fully assembled structural bents into position in a minimum amount of time. Again, highly skilled and experienced personnel are required for these critical lift operations. Of course, ATS had site management and key lead construction personnel that all have deep experience in this type of work.
The balance of the project was then the most manhour intensive portion: remaining structural work, installing the fill splash bars, drift eliminators, mechanical equipment, air inlet louvers, piping and valves. For this work, efficient organization, good housekeeping, safe work practices and optimal crew size were the keys to success. Again, ATS had them all.
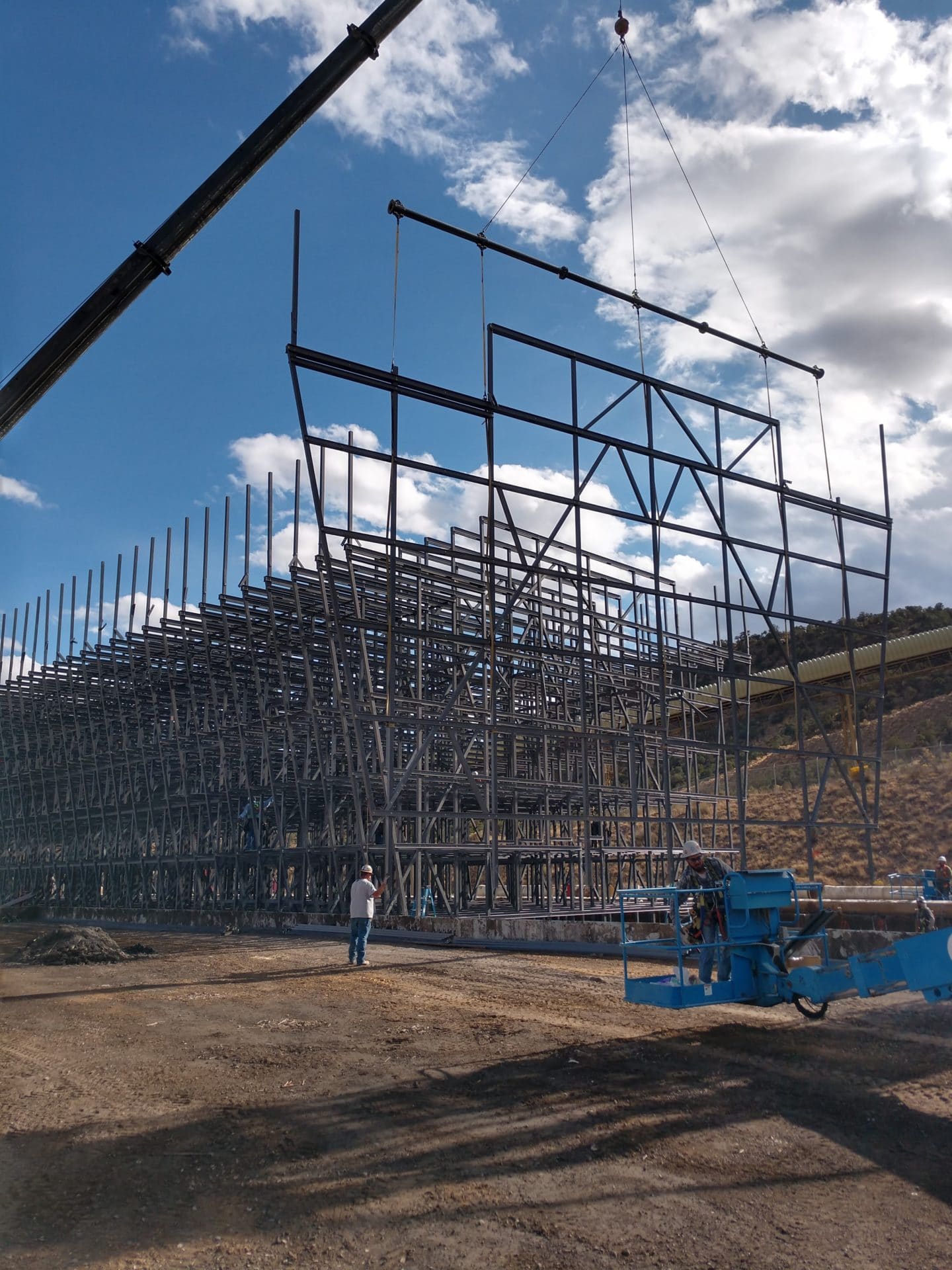
RESULTS
• On Time completion, both phases
• Zero Incidents (Safety and Environmental)
• Expected thermal performance
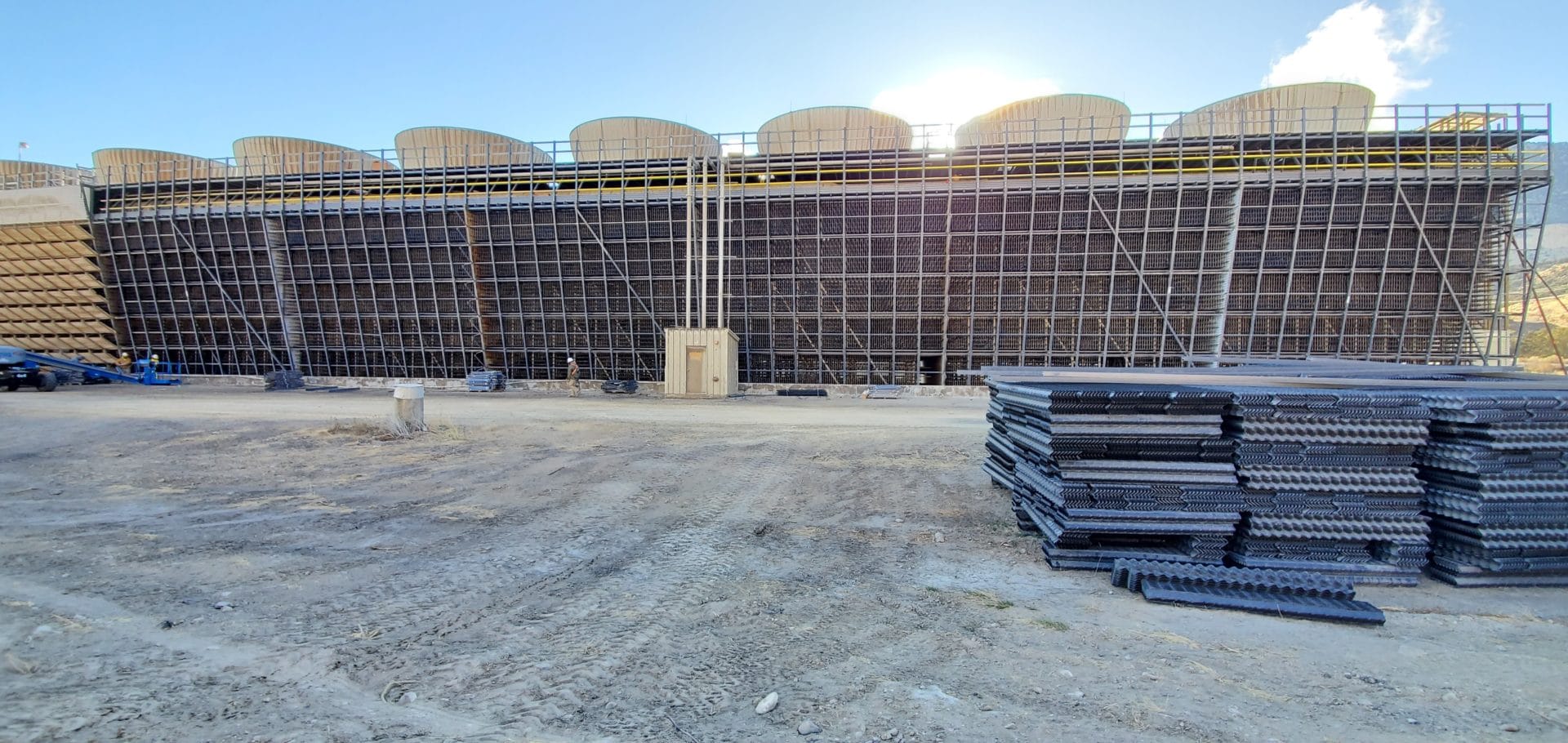